The Art and Science of Tool and Die Casting in Metal Fabrication
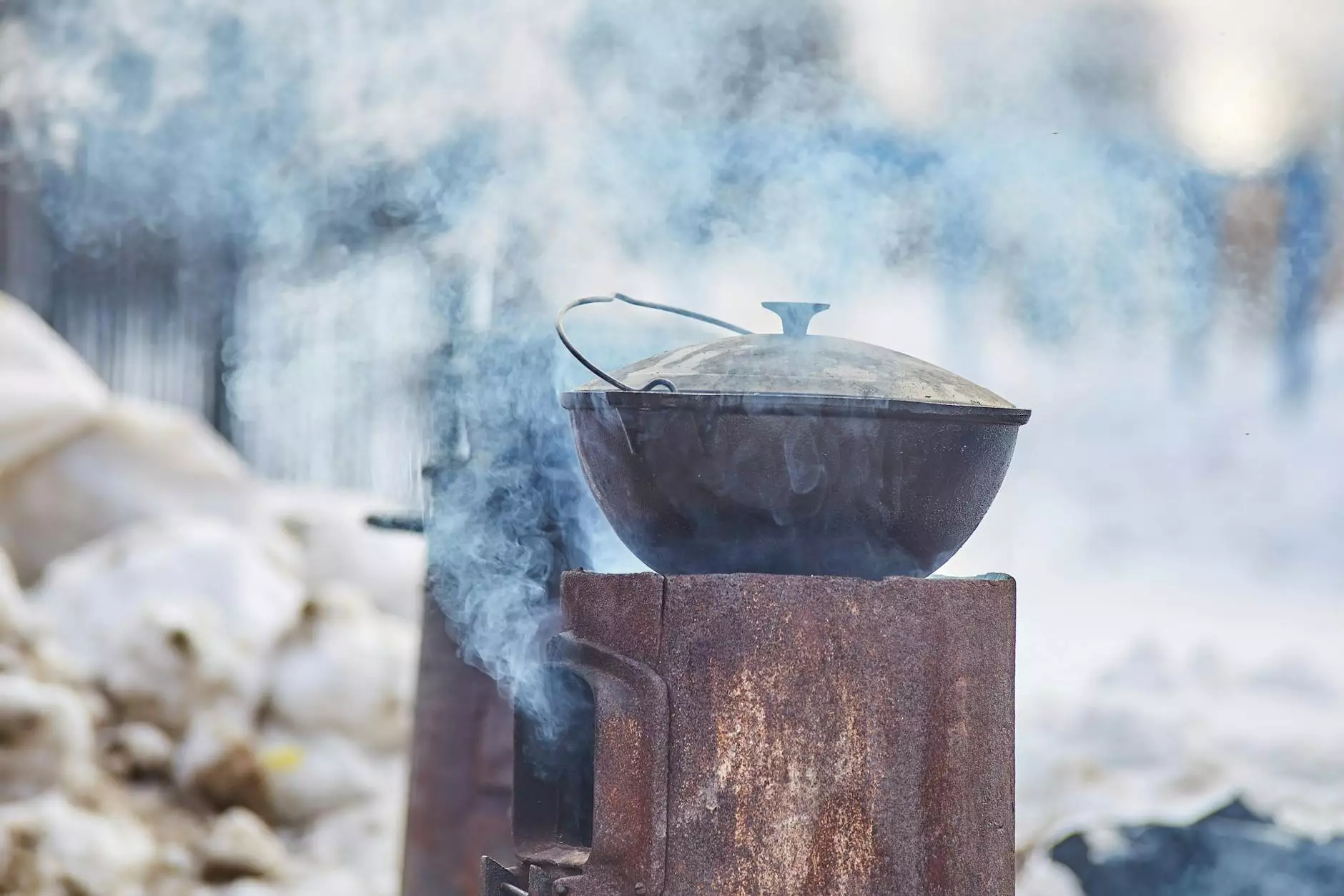
Tool and die casting is an indispensable technique in the world of metal fabrication, playing a pivotal role in producing intricate metal components that meet industry standards. In this comprehensive guide, we will dive deep into the process, benefits, and applications of tool and die casting. We will showcase how Deep Mould, a leader in the realm of metal fabricators, exemplifies excellence in this field.
Understanding Tool and Die Casting
At its core, tool and die casting is a manufacturing process that involves creating precise metal parts through the use of molds. This method is predominantly used for various metals including aluminum, zinc, and magnesium. The casting process enables the production of complex shapes and high tolerances, making it a favored choice among manufacturers.
What is Tool and Die Casting?
The term "tool and die casting" encompasses a range of procedures that convert molten metal into solid components using specialized molds, known as tools or dies. The procedure generally follows these steps:
- Preparation of the Mold: Molds are designed and machined from high-grade materials to withstand extreme temperatures.
- Heating the Metal: The chosen metal is heated until it reaches its molten state, ensuring optimal flow into the die.
- Injection of Metal: The liquid metal is injected into the mold under high pressure, ensuring that every detail is captured.
- Cooling and Solidification: The metal is allowed to cool and solidify within the mold, taking on its desired shape.
- Mold Removal: Once cooled, the die is opened, and the finished parts are ejected.
The Importance of Tool and Die Design
Creating high-quality tools and dies is crucial for the efficiency and accuracy of the casting process. The design phase necessitates thorough planning and innovative engineering techniques to ensure durability and precision. Factors such as mold flow, thermal expansion, and shrinkage rates must be meticulously calculated to prevent defects.
Advantages of Tool and Die Casting
There are numerous advantages to utilizing tool and die casting in manufacturing, making it a preferred choice across various industries:
- High Precision and Tolerances: Tool and die casting allows for the production of parts with exceptional precision, reducing the need for extensive post-processing.
- Complex Geometries: The method can produce complex shapes and designs that would be impractical with other manufacturing techniques.
- Cost-Effectiveness: For high-volume production, the initial investment in die creation is offset by the low cost per unit produced.
- Sustainability: Metal casting can be environmentally friendly, as it often involves the recycling of metals.
- Robust Material Properties: Cast metals often exhibit superior mechanical properties, making them suitable for demanding applications.
Applications of Tool and Die Casting
Tool and die casting has a wide array of applications across different industries. Here are some notable sectors that benefit from this manufacturing technique:
- Automotive Industry: Car manufacturers commonly use tool and die casting for components such as engine blocks, wheels, and transmission housings.
- Aerospace Sector: Aerospace components require lightweight yet incredibly strong materials, making die-cast parts ideal for structural and functional applications.
- Electronics: Many electronic enclosures and heat sinks are fabricated using die casting due to their complex shapes and thermal conductivity.
- Heavy Machinery: Tool and die casting is vital for producing structural components that require high strength and durability.
How Deep Mould Excels in Tool and Die Casting
As a leading name among metal fabricators, Deep Mould has dedicated itself to mastering the art of tool and die casting. Our commitment to excellence is reflected in every aspect of our process:
State-of-the-Art Technology
Deep Mould employs the latest technology in our casting operations. Our machinery is equipped with advanced features that enhance precision and reduce cycle times, ensuring that we deliver fast and reliable results.
Expert Engineering Team
Our team comprises seasoned engineers who specialize in tool and die design. They work diligently to create molds that meet the stringent requirements of our clients while also optimizing production efficiency.
Quality Assurance Programs
Quality is paramount at Deep Mould. We implement rigorous quality control measures throughout the casting process, from the initial design to the final inspection, ensuring that every product meets industry standards.
Customized Solutions
Understanding that each project has unique requirements, Deep Mould offers customized tool and die casting solutions. We collaborate closely with our clients to develop tailored products that fulfill specific specifications and performance expectations.
Future Trends in Tool and Die Casting
The field of tool and die casting is constantly evolving, driven by technological advancements and changing market demands. Here are some trends to watch:
- Automation and AI: The integration of automation and artificial intelligence is set to increase efficiency and minimize human error in the casting process.
- 3D Printing Prototyping: The use of 3D printing for prototype development is streamlining the design phase, allowing for rapid testing of molds before full-scale production.
- Recyclable Materials: The shift towards sustainability is leading to the increased use of recyclable metals in casting, minimizing waste and environmental impact.
Challenges in Tool and Die Casting
Despite its advantages, tool and die casting does present challenges that manufacturers must navigate:
- High Initial Costs: While production costs decrease with volume, the upfront investment for tool creation can be significant.
- Maintenance of Tools: Molds require regular maintenance to ensure they remain functional and precise over time.
- Temperature Control: Precise temperature management is crucial during the melting and casting process to prevent defects.
Conclusion
In conclusion, tool and die casting is a foundational process in the realm of metal fabrication, offering unmatched precision and versatility for a wide range of applications. Companies like Deep Mould are at the forefront of this technology, delivering high-quality solutions that meet the demands of modern industries. As we look to the future, we can expect continued innovation and advancements in this essential manufacturing technique.
If you are seeking a reliable partner for your tool and die casting needs, consider Deep Mould, where quality meets excellence. We are ready to help you bring your projects to life with our expertise in metal fabrication.