Understanding Automotive Injection Mold: A Comprehensive Overview
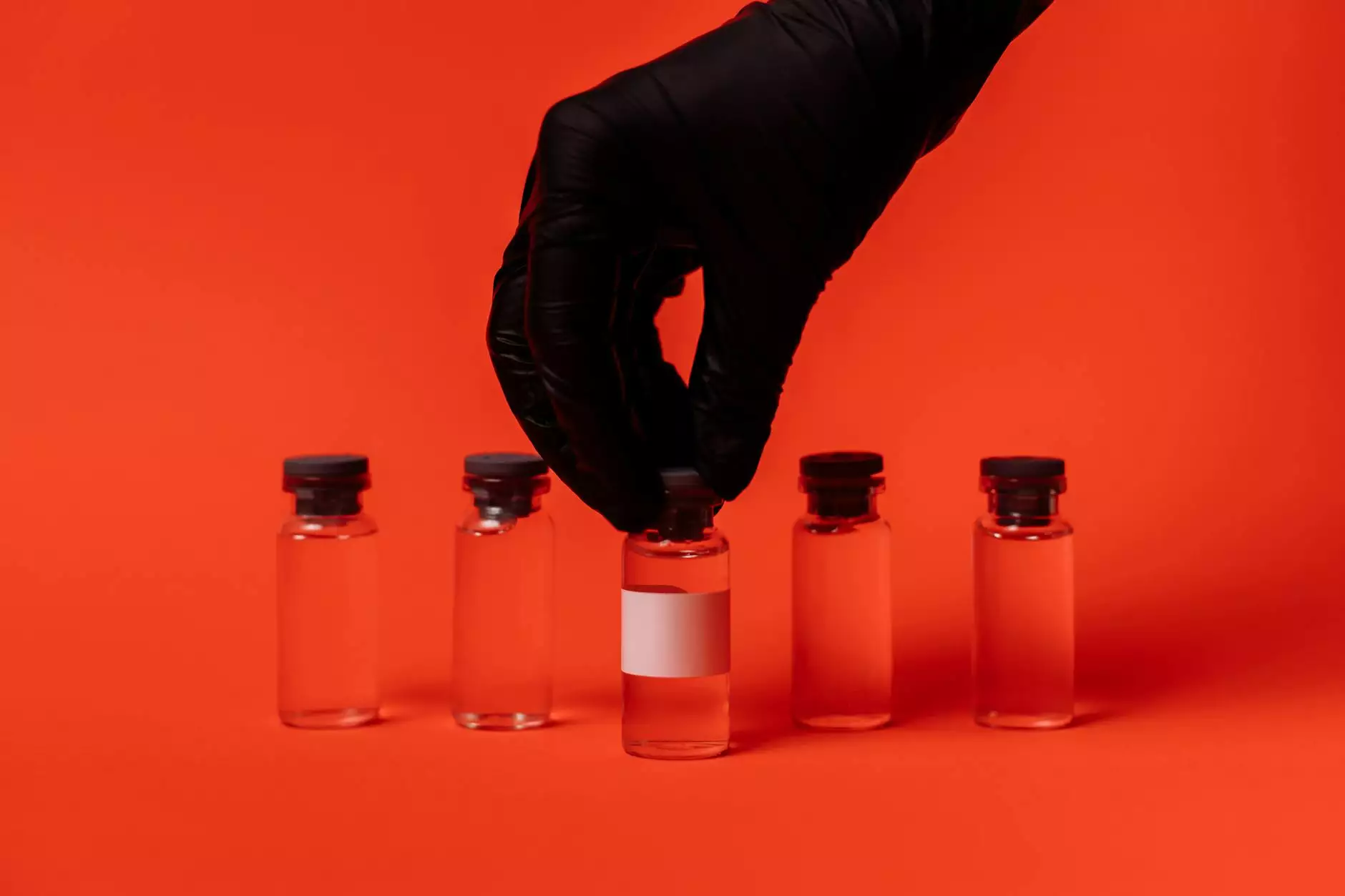
What is Automotive Injection Mold?
Automotive injection mold is a manufacturing process used to produce components for vehicles through the injection of molten material into specially designed molds. This technique has transformed the automotive industry by allowing for the mass production of intricately designed parts with outstanding accuracy and detail. The process involves various stages, including designing the mold, heating the material, injecting it into the mold, and then allowing it to cool and solidify into the final product.
The Importance of Automotive Injection Mold in the Industry
The automotive sector relies heavily on automotive injection mold for several reasons:
- Cost-Effectiveness: This process significantly reduces the cost of manufacturing by allowing for mass production, thus lowering the per-unit price.
- Precision and Consistency: Injection molding enables manufacturers to produce parts with high dimensional accuracy and consistency, which is crucial for vehicle safety and performance.
- Material Efficiency: The process minimizes waste by using only the required amount of material, which is especially important in the environmentally conscious market.
- Complex Designs: Automotive injection molds can create complex geometries that would be difficult or impossible to achieve with other manufacturing methods.
Components of Automotive Injection Mold
Understanding the components used in automotive injection mold is essential for appreciating the process as a whole. These include:
- Mold Base: The fundamental part of the mold, providing support and alignment for the mold components.
- Cavities: The spaces in the mold where the molten material is injected to create the necessary part shapes.
- Core: The part of the mold that defines the internal features of the injected product.
- Sprue: The channel through which the molten material is injected into the mold.
- Gates: The openings that allow the molten material to flow into the mold cavities.
- Cooling System: Integrated systems within the mold that help control the temperature and cooling rate of the injected material, ensuring optimal solidification.
Types of Materials Used in Automotive Injection Mold
The choice of material plays a significant role in the quality and functionality of the final parts produced using automotive injection mold. Commonly used materials include:
- Thermoplastics: Such as ABS and polypropylene, which are widely used due to their durability and ease of processing.
- Thermosetting Plastics: Including epoxy and phenolic resins, known for their high heat resistance and structural stability.
- Metal: Some specialized applications may use metal injection molding for producing high-strength components.
- Composites: These materials combine properties of multiple substances, often improving performance and reducing weight.
The Process of Automotive Injection Molding
The automotive injection mold process can be broken down into several key steps, each critical to ensuring the success of the final product:
- Mold Design: Engineers design the mold based on specifications, considering the material properties and the intended use of the final parts.
- Material Preparation: The raw material is prepared, which may involve heating pellets into a molten state.
- Injection: Using an injection molding machine, the molten material is injected into the mold at high pressure.
- Cooling: The injected material cools and solidifies within the mold. This step is crucial as it defines the part's final properties.
- Part Removal: Once cooled, the mold opens, and the finished part is ejected.
- Finishing: Additional processes such as trimming, painting, or surface treatment may be applied to enhance the part's appearance and functionality.
Benefits of Automotive Injection Molding
The automotive injection mold process offers numerous benefits that make it a preferred choice in automotive manufacturing:
- Speed: The ability to produce large volumes of parts in a short time frame is a significant advantage, especially in high-demand environments.
- Quality Control: Molding technology allows for tight tolerances and high-quality standards, essential for automotive components.
- Versatility: The process can be adapted for a variety of materials, shapes, and sizes, meeting diverse manufacturing needs.
- Reduce Labor Costs: Automated injection molding processes reduce the need for manual labor, further decreasing production costs.
Challenges in Automotive Injection Molding
While the automotive injection mold process is highly effective, it is not without challenges:
- Mold Design Complexity: Designing molds that achieve specific part characteristics can be complex and require advanced engineering expertise.
- Material Limitations: Not all materials are suitable for injection molding; selecting the right material is crucial for achieving desired performance.
- Maintaining Precision: As production scales up, maintaining the precision of molds over time can become challenging.
- Initial Investment: The upfront costs associated with designing and creating molds can be significant, especially for complex components.
Future of Automotive Injection Molding
The future of automotive injection mold looks promising as advancements in technology continue to evolve the manufacturing landscape:
- 3D Printing Integration: The incorporation of 3D printing technologies with traditional injection molding processes could lead to more efficient and customizable production methods.
- Sustainability Initiatives: Companies are increasingly focusing on sustainable manufacturing practices, including using recycled materials in injection molding.
- Smart Manufacturing: The rise of Industry 4.0 is paving the way for smarter factories where real-time monitoring and data analytics can improve efficiency.
- Advanced Materials: Research into new materials that offer enhanced properties, such as lighter weights and better thermal stability, is ongoing.
Why Choose DeepMould.net for Your Automotive Injection Mold Needs?
At DeepMould.net, we pride ourselves on our ability to deliver high-performance automotive injection mold solutions tailored to meet the specific needs of our clients. Here are some reasons to choose us:
- Expertise: Our team consists of industry experts with extensive experience in metal fabrication and injection molding.
- Cutting-edge Technology: We utilize the latest technology to ensure precision and efficiency in every project.
- Customer-Centric Approach: We work closely with our clients to ensure their needs are met, offering customized solutions and exceptional service.
- Quality Assurance: Our rigorous quality control processes guarantee that every part meets the highest standards.
In conclusion, automotive injection mold stands at the forefront of innovation within the automotive industry. Its unique capabilities and benefits make it a vital manufacturing process for producing high-quality automotive components. Whether you are looking to implement injection molding or partner with a reliable supplier, DeepMould.net is here to provide unparalleled service and expertise.